Kugelgewindespindel als tragendes Bauteil
Die Kugelgewindespindel ist das Bauteil eines Kugelgewindetriebes, das die Mutter trägt. Sie ist eine zylindrische Welle und besteht grundsätzlich aus mindestens zwei Teilen. Der eine Teil trägt die schraubenlinienförmige Kugellaufbahn, über die die Bewegungskinematik des Kugelgewindetriebes in ihrer vollständigen Länge umgesetzt wird. Das Spindelgewinde wird dabei im aktuellen Kugelkontaktbereich immer nur sequenziell (partiell, temporär) belastet. Auf dem anderen Teil befinden sich die Spindellagerung und gegebenenfalls der Antriebszapfen. Hier werden die Kräfte und Momente in die Spindel ein- bzw. in die Maschinenumgebung abgeleitet.
Einfluss von Spindellänge und -ausführung
Die Gewindelänge der Spindel wird üblicherweise vom aktiven Verfahrweg der Anwendung, der Gesamtlänge der Mutter (inklusive Abstreifersysteme und sonstigem Zubehör) und dem Gewindeüberlauf bestimmt. Je nach Länge und Ausführung ist die Kugelgewindespindel ein- oder beidseitig gelagert, sodass die Gesamtlänge der Kugelgewindespindel teilweise deutlich länger als die Gewindelänge sein kann. Die Spindelgesamtlänge und die konstruktive Lagergestaltung sind entscheidend für die Knick- und Drehstabilität und somit für die drehzahl- und lastabhängige Einsetzbarkeit des Kugelgewindetriebes.
Die in sehr engen Toleranzen (IT 1, IT 3, IT 5) präzisionsgeschliffene A.MANNESMANN-Kugelgewindespindel ist aus hochfestem Nitrierstahl hergestellt, wobei die gesamte Spindelkontur tiefnitriert ist. Sie hat einen zähen Spindelkern und eine Oberflächenhärte von > 900 HV (= 67 HRC) bei einer Härtetiefe von mindestens 0,4 mm. Diese sehr hohe Oberflächenhärte ist die Grundlage für eine hohe Belastbarkeit und eine lange Lebensdauer.
Konstruktive Festlegung
Die konstruktive Festlegung der Spindelausführung erfolgt üblicherweise durch den Anwender des Kugelgewindetriebes. Sie ist sehr stark von dessen Aufgabenstellung und der Maschinenumgebung abhängig. Die Einflussnahme von A.MANNESMANN als Kugelgewindetriebhersteller fokussiert sich daher meist auf die Optimierung der Funktion und der Herstellungsmöglichkeiten, sowie auf die Sicherstellung der vom Anwender geforderten Qualitäten.
Die Kugelgewindespindel wird charakterisiert durch den Gewindedurchmesser, die Gewindesteigung, die Steigungsrichtung, Kugelgröße, Gewindelänge, die Genauigkeitsklasse und durch das Gewindeprofil sowie die Gangzahl des Kugelgewindes. Dimensionierung und Gestaltung der Lager- und Antriebszapfen richten sich nach den üblichen Abmessungen der Lagerbauarten und deren Befestigungsnotwendigkeiten bzw. nach den Wellen-Naben-Verbindungen der Antriebselemente.
Aufgrund dieser individuellen Gestaltung ist eine Spindelstandardisierung fast nicht möglich.
Verschiedene Spindelbauformen
Aus der konstruktiven Gestaltung und der geometrischen Umsetzung ergeben sich einige grundsätzliche Spindelvarianten, die sich nicht nur technisch, sondern auch wirtschaftlich sehr voneinander unterscheiden. Die einzelnen Unterscheidungsmerkmale sind teilweise sehr erheblich, aber auch nicht immer direkt offensichtlich.
Unabhängig, ob die Kugelgewindespindel angetrieben oder nicht drehend ausgeführt ist, können bestimmte Funktions- oder Herstellungsgründe Sonderbauformen erfordern, die nicht einer „normalen" Vollspindel entsprechen. Hierzu zählen die Spindelausführungen wie:
- Hohlspindeln
- Bundspindeln
- gekuppelte Spindeln
- korrosionsbeständige Spindeln
Damit auch diese Kugelgewindespindeln in hoher Qualität gefertigt werden können, müssen bei der Herstellung von Kugelgewindespindeln in Sonderbauformen neben der ohnehin erforderlichen Sorgfalt, auch teilweise sehr unterschiedliche, spezifische Einflüsse berücksichtigt werden. Bei der Anwendung derartiger Kugelgewindespindeln kann es zu gewissen bauartbedingten Einschränkungen kommen.
Vollspindeln
Die meisten Kugelgewindespindeln werden als Vollspindel ausgeführt. Der Spindelquerschnitt entspricht dabei dem eines Vollzylinders (ohne Bohrung). Die Kraftübertragung erfolgt über die gesamte Querschnittsfläche bei entsprechenden Zug-, Druck- und Torsionsspannungen.
Da der erforderliche Bearbeitungsaufwand am geringsten ist, ist die Vollspindel herstellungstechnisch nicht nur die einfachste, sondern auch die kostengünstigste Ausführungsmöglichkeit.
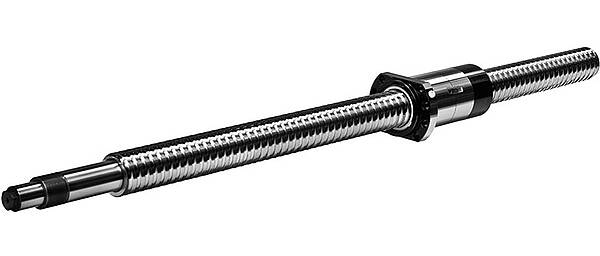
Hohlspindeln
Soll die Spindelmitte z. B. für Kühl- oder Schmieraufgaben mit einer zentrischen Bohrung versehen werden oder es müssen andere Funktionsbauteile in diesem Raum eingebaut werden , so kann die Kugelgewindespindel auch als Hohlspindel ausgeführt werden. Der Spindelquerschnitt entspricht in diesem Falle dem eines Rohres mit entsprechender Wandung. Die Rohrwandung muss jedoch mindestens so dimensioniert sein, dass die Axiallast und das Drehmoment unter Berücksichtigung der Gewinderillentiefe verformungsfrei und sicher übertragen werden kann.
Vorteile von Hohlspindeln
Der Einsatz von Hohlspindeln hat verschiedene technische Vorteile. Zum Beispiel lässt sich die biegekritische Drehzahl durch Hohlbohren der Spindel weiter erhöhen. Interessant dabei ist, dass bei sonst konstanten Spindelabmessungen mit steigendem Innendurchmesser der Spindel die biegekritische Drehzahl ständig wächst. Es gibt theoretisch keinen Sättigungspunkt, ab dem die biegekritische Drehzahl nicht mehr ansteigt. Problematisch ist natürlich die genaue Fertigung solcher Hohlspindeln. Vorteilhaft ist auch das geringere Massenträgheitsmoment von Hohlspindeln.
Wird eine Fest-Fest-Lagerung eingesetzt, so besteht die Möglichkeit, die Bohrung der Hohlspindel für ein Kühlmedium zu nutzen, um die Spindeltemperatur während des Bearbeitungsvorgangs möglichst konstant zu halten. Dadurch werden die notwendigen Reckkräfte minimiert und Steigungsfehler der Spindel infolge Wärmedehnung herabgesetzt.
Wird der Spindelkörper nicht wie herkömmlich fest-los- sondern fest-fest-gelagert und zusätzlich hohlgebohrt, so wird der Axialsteifigkeitsverlust infolge des Hohlbohrens durch die Fest-Fest-Lagerung mehr als ausgeglichen.
Hohlspindeln haben im Vergleich zu entsprechenden Vollspindeln geringere Massen, geringere Steifigkeiten und meist allerdings nur geringfügig geringere Massenträgheitsmomente.
Da die Innenkontur der Hohlspindel meist bereits vor der Warmbehandlung gefertigt wird, ist diese dann auch entsprechend hart (nitriert). Auch die temperaturbedingten Geometrieveränderungen von Hohlspindeln während der Fertigung sind aufgrund der geringeren Massen größer. Dies führt zu einer Vergrößerung des Durchmessers und vor allem zu einer Verlängerung der Spindel, durch die auch die Gewindesteigung beeinflusst werden kann. Hohlspindeln sind in der Regel deutlich bearbeitungsintensiver und damit in der Herstellung auch kostspieliger.

Bundspindeln
Üblicherweise ist der Außendurchmesser der Kugelgewindespindel der größte Durchmesser, aus dem alle sonstigen Spindelkonturen herausgearbeitet werden. Unter bestimmen Voraussetzungen kann es aber erforderlich werden, in einzelnen Spindelbereichen größere Durchmesser als den Außendurchmesser des Kugelgewindes nutzen zu müssen. Dies kann z. B. der Wunsch sein, eine vergrößerte Anlageschulter für ein Spindellager zu erhalten und / oder mehr Steifigkeit und Stabilität in der Spindelwelle zu erzielen. Solche Spindeln werden als Bundspindeln bezeichnet.
Wegen des einseitig größeren Spindeldurchmessers können die Kugelgewindemuttern bei Bundspindeln nur von einer Seite montiert werden. Bundspindeln können den größeren Spindeldurchmessern auch in der Spindelmitte haben. Bei dieser Ausführung verfügt die Spindel dann z. B. meist wechselseitig über ein rechtsgängiges und ein linksgängiges Kugelgewinde und ist mit zwei Muttern ausgestattet. Der größte Spindeldurchmesser in der Spindelmitte wird gegebenenfalls auch zur Aufnahme einer Stützlagerung benutzt.
Da oftmals aus Gründen der Materialdisposition der Außendurchmesser des nächstgrößeren Nenndurchmessers als Ausgangsgröße gewählt werden muss, ist der notwendige Zerspanungsaufwand zur Herstellung einer solchen Spindel beträchtlich. Außerdem ist der Bund auch beim Schleifen des Kugelgewindes störend.
Erhöhter Herstellungsaufwand
Wenn die Kosten für diesen Mehraufwand größer sind als die Materialmehrkosten, so ist die Herstellung einer größeren Spindel meist wirtschaftlicher. Bei größeren Spindeln ist allerdings zu berücksichtigen, dass sich gleichzeitig auch die Einbaumaße der Mutter vergrößert und dieser erhöhte Platzbedarf im zur Verfügung stehenden Einbauraum vorhanden sein muss.
Hülsen und Ringe als Alternative
Um die Notwendigkeit einer Bundspindelausführung zu umgehen, können je nach Zielsetzung (z. B. bei vergrößerter Anlageschulter für die Lagerung) anstelle des Bundes auch Hülsen oder Ringe vorgesehen werden. In diesen Fällen wird die stabile Anlageschulter durch diese Ringe, die nach dem Schleifen des Gewindes montiert werden, hergestellt. Diese Bauteile können entweder lose aufgefädelt, geklebt oder aufgeschrumpft werden.
Der Vorteil geklebter Stützringe ist, dass diese bis kurz vor der endgültigen Verklebung noch feinjustiert werden können. Zum Kleben wird meist der Klebstoff Loctite 603 verwendet. Die Klebung kann durch entsprechende Wärmezufuhr auch gut wieder gelöst werden. Um zu vermeiden, dass Klebstoff in die Gewindeumläufe oder in die Mutter gelangt, ist bei der Verklebung darauf zu achten, dass nur die Bohrungsoberfläche und nicht die Stirnfläche mit Klebstoff benetzt wird.
Bei aufgeschrumpften Stützringen muss unbedingt darauf geachtet werden, dass der Ring gut und spaltfrei an der Anlagekante anliegt, da er nachträglich nicht mehr ausgerichtet bzw. verschoben werden kann. Eine Demontage des Ringes ist nur mit Zuhilfenahme großer Kräfte und meist nicht zerstörungsfrei möglich. Wegen der deutlich höheren Herstellkosten, sollten Bundspindeln nur dann zum Einsatz kommen, wenn es technisch absolut notwendig ist und es keine praktikable Alternativlösung gibt.

Gekuppelte Spindeln für Überlängen bis 25 m
Die maximale Länge einer Kugelgewindespindel ist meist durch die Verfügbarkeit des Ausgangsmaterials und die Fertigungsmöglichkeiten (z. B. schleifen, nitrieren) begrenzt. Um bei Bedarf trotzdem längere Spindeln herstellen zu können, besteht auch die Möglichkeit, zwei Spindeln fest zu kuppeln. Hierbei werden zwei fertig geschliffene Spindeln so ausgerichtet, dass die Gewindegänge exakt ineinander übergehen. Die Gewinde werden dabei nicht als Schraubverbindung, sondern als verkrallende Gegenhaltungen des Vergussmaterials (SKC) genutzt. Die verkrallende Wirkung wird dabei durch die gegenläufige Steigungsrichtung (rechts- und linksgängig) zusätzlich verstärkt.
Die so ausgerichteten Spindeln werden durch eine eigens hierfür entwickelte Kuppelstelle formschlüssig verbunden. Wenn die Wegabweichungen der beiden Spindelstücke nahezu identisch sind, entstehen durch gekuppelte Spindeln üblicherweise keine nennenswerten Qualitätsminderungen. Theoretisch lassen sich durch mehrere Kuppelstellen beliebig lange Spindeln herstellen.

Für die Auslegung und Bewertung der Kuppelstelle sind genaue Kenntnisse des Kugelgewindetriebeinsatzes und des vorliegenden Kraftflusses von großer Wichtigkeit. Bei Kugelgewindetrieben mit angetriebenen Muttern wird die Kuppelstelle meist nur durch die auftretende Axialkraft belastet. Wird die Spindel angetrieben, so kommt als Belastung zusätzlich zur Axialkraft das Antriebsdrehmoment in der Spindel hinzu.
Bitte beschreiben Sie uns Ihren Anwendungsfall. Unsere Experten beraten Sie individuell.
Einsetzbarkeit
Gekuppelte Kugelgewindespindeln werden üblicherweise nur in horizontaler Lage eingesetzt. Aufgrund der möglichen axialen Zugbelastung werden von A.MANNESMANN aus Sicherheitsgründen vertikal hängende Kugelgewindespindeln nicht in gekuppelter Ausführung hergestellt.
Gewindelänge
Die Gewindelänge einer Kugelgewindespindel ist bestimmend für die Gesamtlänge einer Kugelgewindespindel. Sie setzt sich aus dem Nutzweg, dem beidseitigen Überlaufen und der Länge des Mutternkörpers zusammen. Der Nutzweg lu ist dabei der maximal mögliche verfahrbare Weg der Mutter, über den die geforderte Genauigkeit anwendbar ist. Er sollte größer bemessen sein, als der konstruktiv vorgesehene, nominelle Verfahrweg der Achse und wird meist durch Endanschläge und / oder durch Endschalter begrenzt. Der steigungsabhängige Überlauf le hat keine Genauigkeitsanforderung, da er üblicherweise nicht befahren wird. Bei der Mutterlänge l2 müssen gegebenenfalls auch die Baulängen für Abstreifer berücksichtigt werden.
Spindeldetails
Um die Funktionalität und die Qualität einer Kugelgewindespindel vollständig sicherzustellen, sind bei der Spindelherstellung diverse Details zu berücksichtigen, die dem Kugelgewinde nur teilweise oder gar nicht zugeordnet werden können. Hierzu zählen z. B.:
- Lagersitze
- Aufnahmesitze für Antriebsbauteile
- Gewindeausläufe
- Freistiche
- Zentrierungen
- Befestigungsgewinde
- stirnseitige Gewindebohrungen
- Schlüsselflächen
- Drehgeberanschlüsse
Genauigkeit der Gewindespindel
Die Genauigkeit eines Kugelgewindetriebes wird durch die Gewindesteigung und der damit verbundenen Wegabweichung bezogen auf den Verfahrweg bestimmt. Die Wegabweichung der Mutter ist dabei immer geringer als der Steigungsfehler im Kugelgewinde der Spindel, da die Steigungstoleranz der Mutter die Auswirkung des Spindelsteigungsfehlers etwas dämpft. Diese Genauigkeit entscheidet letztlich über die Verwendbarkeit des Kugelgewindetriebes als Positionier- oder Transport-Kugelgewindetrieb.